Latest News
FP McCann’s StormHoldTM pipe tank offers the ideal stormwater attenuation solution for housing development in Farnley, Leeds
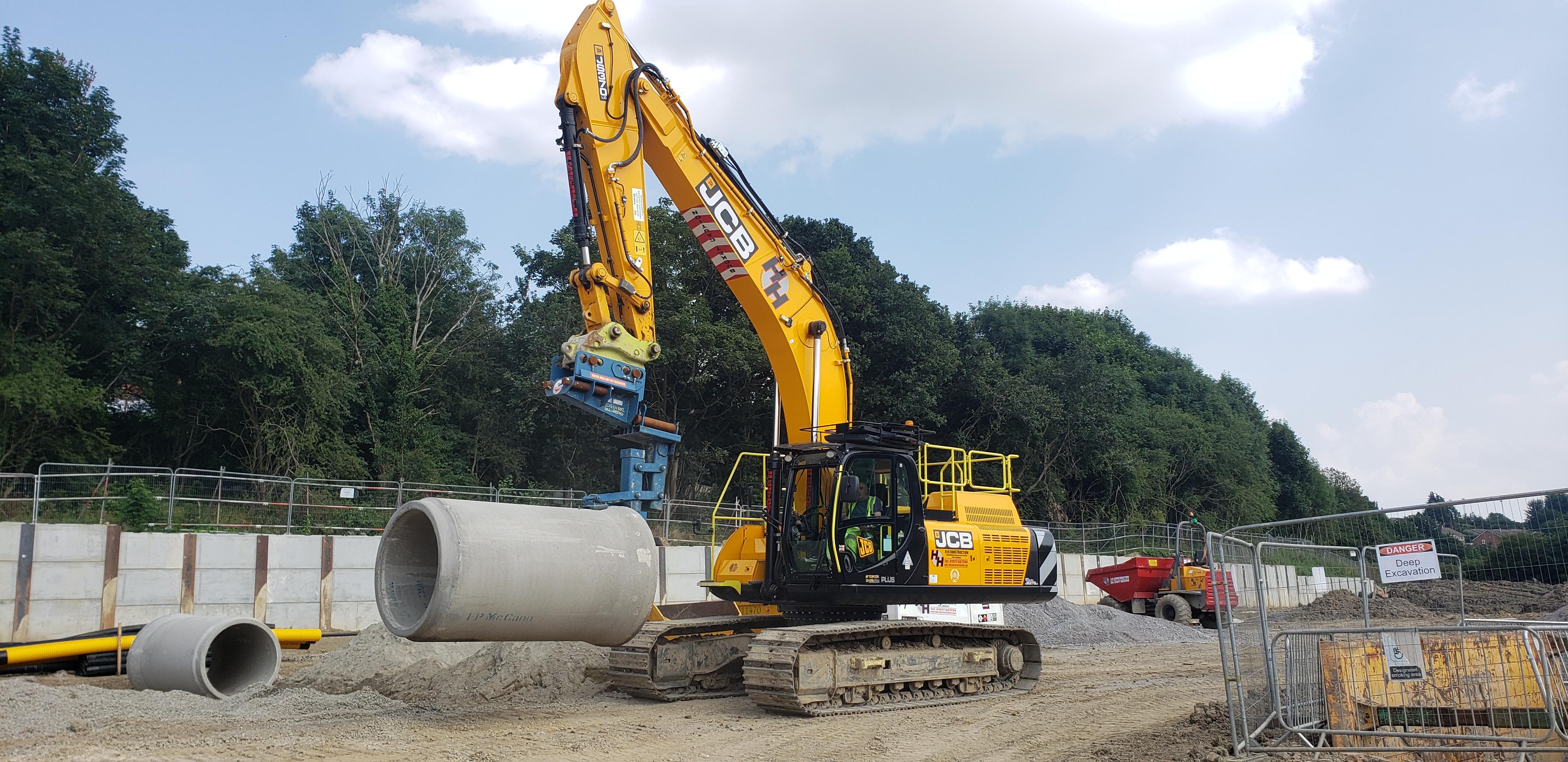
When faced with the challenge of installing a stormwater attenuation system strong enough to sustain variable traffic loads, and durable enough to serve over the lifetime of the housing development it serves, HH Construction had no illusions about the best attenuation system for the job.
The Stonebridge Mills housing development scheme will see 82 new homes constructed at the site of the Grade II derelict mills in Farnley, Leeds. The new housing development is expected to be completed, and ready for its residents, by summer 2023. Civil Engineering and groundwork contractors, HH Construction and Castleford groundworks, were tasked with constructing the on-site drainage and road infrastructure for the new housing development. This included construction of a storm water attenuation system to mitigate flood risks on site. They needed an attenuation solution robust enough to take variable traffic loads beneath the development's main access road and capable of functioning throughout the 100+ years lifespan of the development.
After considering several attenuation solutions, drainage designers Fairhurst decided to specify a FP McCann's StormHold TM DN1200 precast pipe tank solution. StormHold™ Concrete pipeline tanks can be designed to different traffic loading requirements, as high as LM1 if needed, and are manufactured to BS 5911-1, which offers a path for a 100 years intended working life. A key feature in the attenuation system installed was the use of bespoke side entry manhole bends, incorporated as an integral part of the online system, to remove the need for separate manhole builds. Up to nine of these side-entry units were used in the attenuation tank system with pipe bends ranging from 10° to 160°.
Commenting on their choice for stormwater attenuation, Steve Kelly, planner for HH Construction noted that after considering alternative systems, taking into account the need to install the system beneath a road "...the use of FP McCann's DN1200 precast concrete pipes was considered by far the best option”. The use of manhole bends, eliminating the need for manholes, was also one of the main reasons why StormHold™ was the contractors' and designers' preferred option.
Read more
The Stonebridge Mills housing development scheme will see 82 new homes constructed at the site of the Grade II derelict mills in Farnley, Leeds. The new housing development is expected to be completed, and ready for its residents, by summer 2023. Civil Engineering and groundwork contractors, HH Construction and Castleford groundworks, were tasked with constructing the on-site drainage and road infrastructure for the new housing development. This included construction of a storm water attenuation system to mitigate flood risks on site. They needed an attenuation solution robust enough to take variable traffic loads beneath the development's main access road and capable of functioning throughout the 100+ years lifespan of the development.
After considering several attenuation solutions, drainage designers Fairhurst decided to specify a FP McCann's StormHold TM DN1200 precast pipe tank solution. StormHold™ Concrete pipeline tanks can be designed to different traffic loading requirements, as high as LM1 if needed, and are manufactured to BS 5911-1, which offers a path for a 100 years intended working life. A key feature in the attenuation system installed was the use of bespoke side entry manhole bends, incorporated as an integral part of the online system, to remove the need for separate manhole builds. Up to nine of these side-entry units were used in the attenuation tank system with pipe bends ranging from 10° to 160°.
Commenting on their choice for stormwater attenuation, Steve Kelly, planner for HH Construction noted that after considering alternative systems, taking into account the need to install the system beneath a road "...the use of FP McCann's DN1200 precast concrete pipes was considered by far the best option”. The use of manhole bends, eliminating the need for manholes, was also one of the main reasons why StormHold™ was the contractors' and designers' preferred option.
Concrete Pipe Structural Calculator Updated
The concrete pipe structural design calculator, an online tool used by thousands of engineers every year, has been updated to the new national pipeline design methodology in BS 9295:2020.
BS 9295, first published 11 years ago as a complementary guidance to European Standard EN 1295, became the main national pipeline structure design standard in the UK when it was revised and published last year. Significant changes were introduced to the design of both rigid and flexible pipeline systems. This has prompted a revamp of our structural design calculator. The calculator can now enable pipeline design calculations based on both, wide and narrow trench conditions. The Design Load tables associated with the calculator were also updated and aligned with Eurocode loading requirements. In line with BS 9295, the new calculator only accounts for two main types of conditions overground: “Main Road” and “Field”. We have also made the calculator more user- friendly and calculation results can now be exported in a PDF or Excel document format.
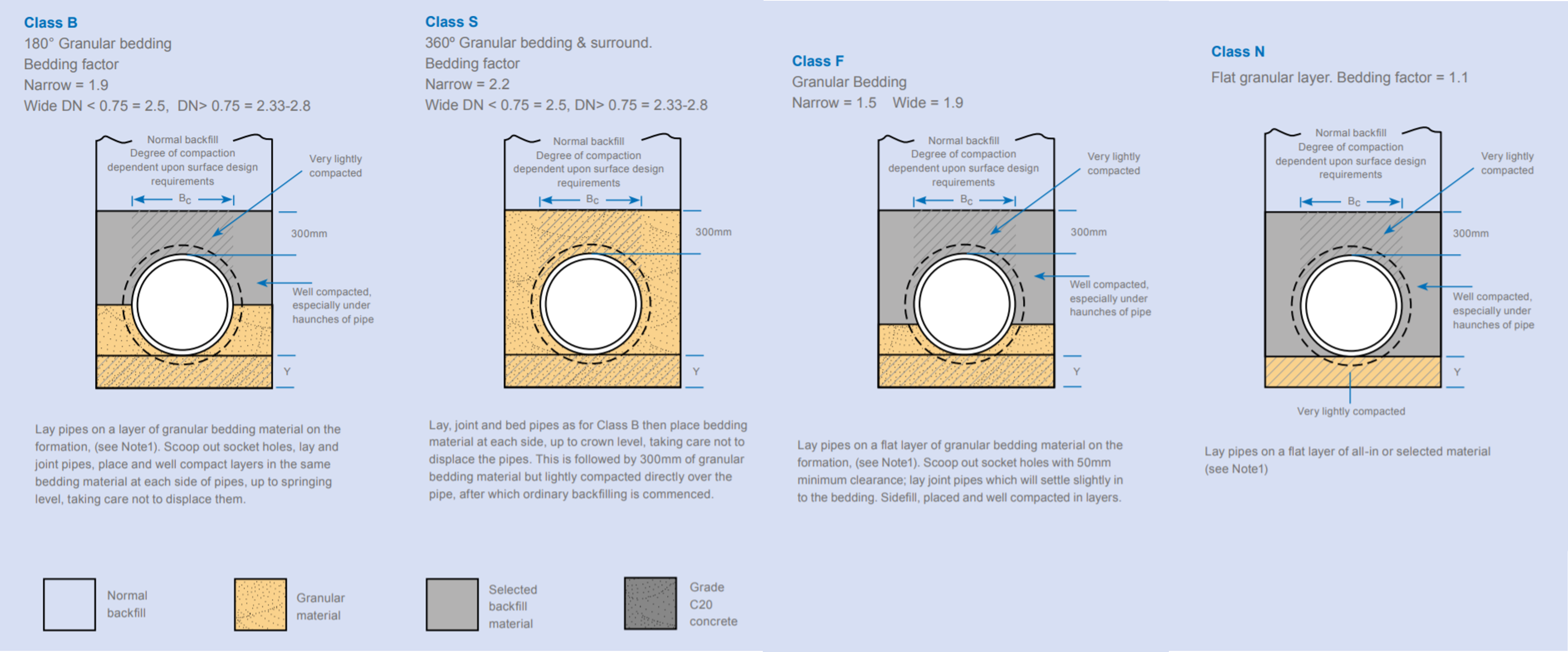
The new structural calculator can be found at the BPDA website here: https://www.precastdrainage.co.uk/calculators/structural-design
For more information on BS 9295:2020 and how it has affected the structural design of concrete pipeline systems, please visit this blog at BPDA website: https://precastdrainageblog.co.uk/2019/11/buried-pipeline-design-standard-brought-up-to-date/
Read more
BS 9295, first published 11 years ago as a complementary guidance to European Standard EN 1295, became the main national pipeline structure design standard in the UK when it was revised and published last year. Significant changes were introduced to the design of both rigid and flexible pipeline systems. This has prompted a revamp of our structural design calculator. The calculator can now enable pipeline design calculations based on both, wide and narrow trench conditions. The Design Load tables associated with the calculator were also updated and aligned with Eurocode loading requirements. In line with BS 9295, the new calculator only accounts for two main types of conditions overground: “Main Road” and “Field”. We have also made the calculator more user- friendly and calculation results can now be exported in a PDF or Excel document format.
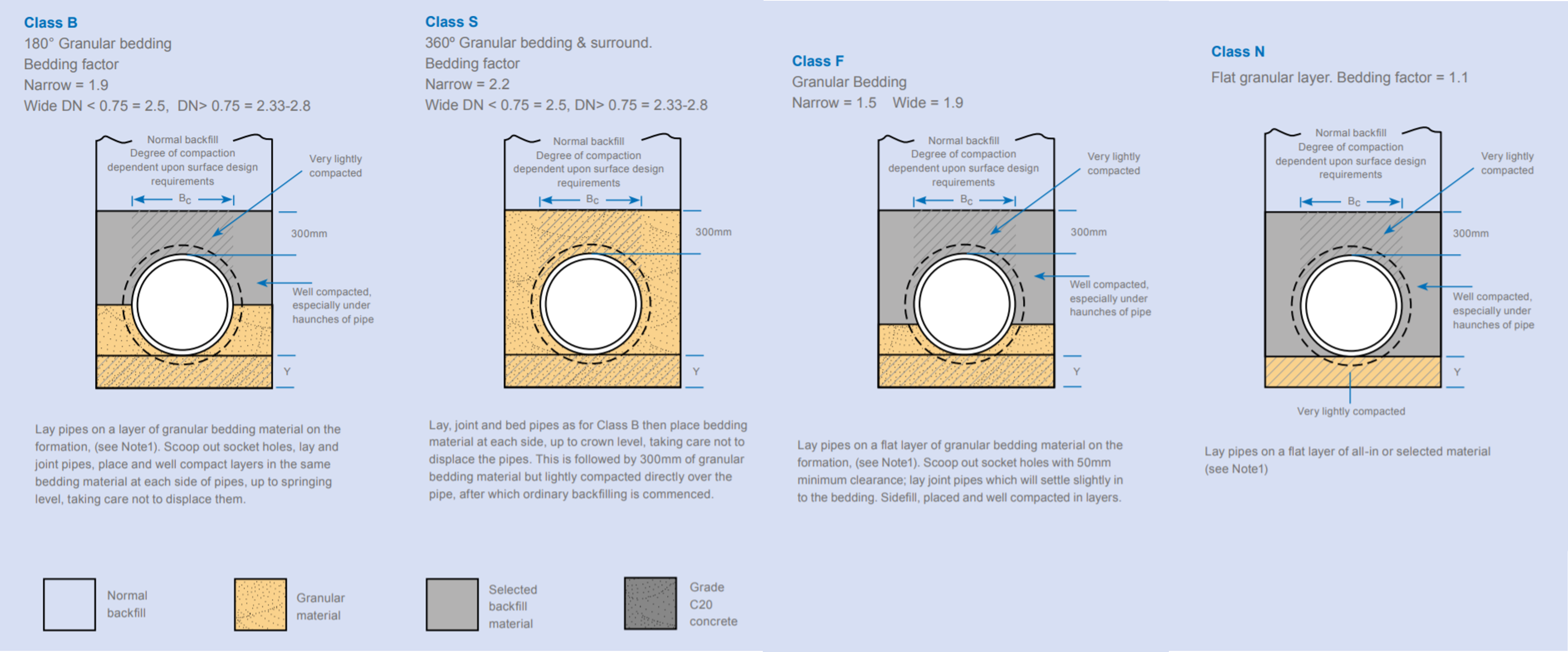
The new structural calculator can be found at the BPDA website here: https://www.precastdrainage.co.uk/calculators/structural-design
For more information on BS 9295:2020 and how it has affected the structural design of concrete pipeline systems, please visit this blog at BPDA website: https://precastdrainageblog.co.uk/2019/11/buried-pipeline-design-standard-brought-up-to-date/
Marshalls’ Box culvert attenuation tank installed in record time for industrial units in Skelton-in-Cleveland, Teesside
Two week was the time it took Castlehouse Construction to install the 250m3 box-culvert attenuation tank serving three industrial units at Skelton-in-Cleveland, Teesside.
The Marshalls box culvert attenuation tank was installed under the car park serving the three building materials and tool supplier business. Casltehouse Construction's £7 million contract included construction of the entire retail park area and Marshalls' MC2010 precast concrete box culverts were chosen as the best option for surface water and rainwater attenuation. 32 precast box culverts units were laid in a double run to create the underground attenuation tank. With a Design Life of 120 years, the units would offer a long-lasting solution capable of undertaking various loads from trucks and other HGVs expected to use the car park on a frequent basis.
The attenuation tank was installed in no more than a week, with another week to finalise and finish the entire job. Billy Fairhurst, Marshalls' Business Development Manager (Special Projects) referred to the fact that almost two thirds of the units used were already available from stock "Being able to use a stock product allowed us to speed up the programme". Only around 12 box culvert units were bespoke or required some customisation to meet the project's requirements.
Castlehouse Construction Project Manager, Dave Crozier, praised Marshalls Civils & Drainage for their support throughout the process, "Marshalls Kept us fully up-to-date with the manufacture of the specials and provided helpful advice to make the installation easier". In addition to the car park, the project also included some soft and hard landscaping.
For more information on the project, please visit Marshalls website here. You can also find out more about box culverts' use in stormwater attenuation here.
Read more
The Marshalls box culvert attenuation tank was installed under the car park serving the three building materials and tool supplier business. Casltehouse Construction's £7 million contract included construction of the entire retail park area and Marshalls' MC2010 precast concrete box culverts were chosen as the best option for surface water and rainwater attenuation. 32 precast box culverts units were laid in a double run to create the underground attenuation tank. With a Design Life of 120 years, the units would offer a long-lasting solution capable of undertaking various loads from trucks and other HGVs expected to use the car park on a frequent basis.
The attenuation tank was installed in no more than a week, with another week to finalise and finish the entire job. Billy Fairhurst, Marshalls' Business Development Manager (Special Projects) referred to the fact that almost two thirds of the units used were already available from stock "Being able to use a stock product allowed us to speed up the programme". Only around 12 box culvert units were bespoke or required some customisation to meet the project's requirements.
Castlehouse Construction Project Manager, Dave Crozier, praised Marshalls Civils & Drainage for their support throughout the process, "Marshalls Kept us fully up-to-date with the manufacture of the specials and provided helpful advice to make the installation easier". In addition to the car park, the project also included some soft and hard landscaping.
For more information on the project, please visit Marshalls website here. You can also find out more about box culverts' use in stormwater attenuation here.
Inside Stanton Precast’s Green revolution
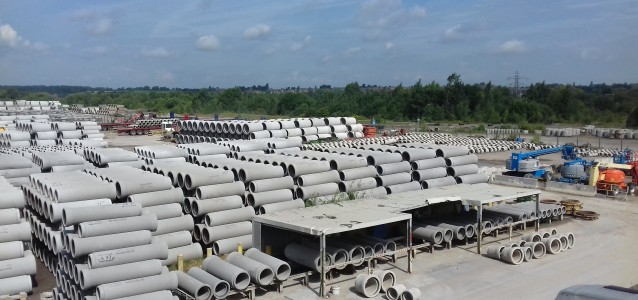
Like many other British precast concrete manufacturers, Stanton Precast has a long-standing ambition to become a low carbon product manufacturer and help the concrete sector reach Net Zero by 2050. Over the last few years, the company has introduced a wide range of measures to address carbon and reduce energy consumption and raw material use to a minimum in what can only be described as a Green Revolution.
This short case study offers a glimpse into the company’s own Green Revolution where measures were introduced to reduce both carbon and raw material use:
Reduced Energy Consumption
Stanton Precast has long been using a renewable energy source for its factory’s electricity supply, reducing its manufacturing carbon emissions by almost a third. But the company isn’t satisfied with this achievement alone and have sought help from energy consultants to explore how its energy consumption can be further reduced and become less dependant on fossil fuels. The ambitious scheme saw a wide range of measures introduced: from switching the entire lighting system to LED, to the introduction of energy saving elements such as motion detection lighting.
The company has an energy monitoring and benchmarking programme, as part of its ISO 14001 accredited management system, to ensure that further gains can be achieved on a regular basis.
Recycle and Reuse Materials
Stanton Precast has a long history of innovation in production and use of raw materials. The company currently replaces a proportion of its virgin aggregate with recycled variants obtained via the crushing and grading of the company’s own waste product. This wouldn’t only reduce the use of virgin material but can also result in significant carbon savings associated with waste processing and sourcing of virgin material.
Progress is monitored via a weekly graph sent to key managers detailing target versus actual usage percentages.
Capture and Reuse Rainwater and waste
Stanton Precast has recently installed two rainwater-harvesting systems to its batching plant and wet cast shed. The system collects rainwater from the roofs and stores it in dedicated tanks where it is then re-used in the concrete production process.
A similar reuse strategy is also being implemented with other waste materials. Stanton Precast currently diverts 93% of its waste from landfills. For example, all timber is reused where possible (i.e. bearers are returned via the hauliers after delivery and used again until beyond economical repair) and where not possible is sent via a waste carrier for recycling.
The last few years saw an increase in carbon reduction initiatives and measures by other precast drainage manufacturers as well. Between 2016 and 2019, BPDA believes that the carbon footprint of an average concrete pipe has dropped by anything between 6% to 9%. With further efforts by companies such as Stanton Precast, and with the introduction of the new BS 5911, which allows for low-carbon mixes, we would expect further significant drops in the carbon footprint of concrete pipes to the next few years.
Revised standard aims to make concrete pipes more resilient
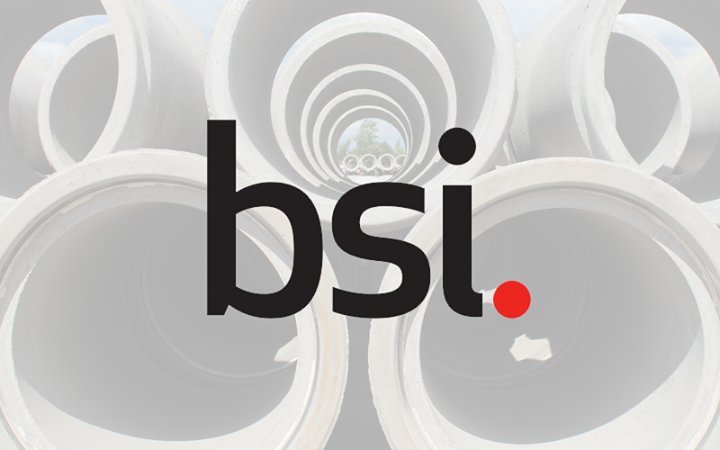
BSI has published BS 5911-1: 2021, Specification for unreinforced and reinforced concrete pipes. The revised specification standard will enable a wider variety of low carbon cements. It also introduces additional high-pressure jetting test requirements and, for the first time, makes a clear reference to requirements to meet a 100 years intended working life for concrete pipes.
The standard was last revised around 11 years ago. However, with calls across the industry for more infrastructure resilience and serviceability, a number of new requirements were introduced to help with the specification of more durable concrete pipeline systems capable of withstanding future challenges and requirements for further resilience. The new standard introduces a clearer link to the need to specify a DC-4 exposure class mix to meet the requirement for a 100 years’ Intended Working Life for pipes. That link already existed in the past as all precast drainage is already specified to standards such as Special Digest 1 “Concrete in Aggressive Grounds” and BS 8500. But following the latest amendment, that link between Design Chemical exposure class and the pipes’ Intended Working Life is made more evident. The direct reference to a 100 years working life would not only help with Whole Life Carbon and cost planning, but also with Design for Circular Economy and long-term performance.
The “Cementitious Content” section of BS 5911-1 has now been amended and will now enable the use of a significantly wider variety of low carbon cements, including low carbon cements added recently to the concrete specification standard, BS 8500, such as pozzolanic cements and a variety of ternary cements with limestone fines content.
With the rise in fatbergs and sewer blockage problems, authors of the standard also introduced new testing requirements to ensure pipeline robustness during maintenance and high-pressure sewer jetting operations. A new annex on stationary water jetting tests was introduced where pipeline products will be tested using a 28 Mpa (approx. 4,000 psi) water jet pressure. This new testing requirement will offer assurance that every concrete pipe manufactured in the UK is robust enough to undertake the level of high-pressure jetting normally needed to remove fatbergs.
The new BS 5911-1: 2021 can be purchased from the BSI website. For any further information on the new standard please contact email@precastdrainage.co.uk
Read more
The standard was last revised around 11 years ago. However, with calls across the industry for more infrastructure resilience and serviceability, a number of new requirements were introduced to help with the specification of more durable concrete pipeline systems capable of withstanding future challenges and requirements for further resilience. The new standard introduces a clearer link to the need to specify a DC-4 exposure class mix to meet the requirement for a 100 years’ Intended Working Life for pipes. That link already existed in the past as all precast drainage is already specified to standards such as Special Digest 1 “Concrete in Aggressive Grounds” and BS 8500. But following the latest amendment, that link between Design Chemical exposure class and the pipes’ Intended Working Life is made more evident. The direct reference to a 100 years working life would not only help with Whole Life Carbon and cost planning, but also with Design for Circular Economy and long-term performance.
The “Cementitious Content” section of BS 5911-1 has now been amended and will now enable the use of a significantly wider variety of low carbon cements, including low carbon cements added recently to the concrete specification standard, BS 8500, such as pozzolanic cements and a variety of ternary cements with limestone fines content.
With the rise in fatbergs and sewer blockage problems, authors of the standard also introduced new testing requirements to ensure pipeline robustness during maintenance and high-pressure sewer jetting operations. A new annex on stationary water jetting tests was introduced where pipeline products will be tested using a 28 Mpa (approx. 4,000 psi) water jet pressure. This new testing requirement will offer assurance that every concrete pipe manufactured in the UK is robust enough to undertake the level of high-pressure jetting normally needed to remove fatbergs.
The new BS 5911-1: 2021 can be purchased from the BSI website. For any further information on the new standard please contact email@precastdrainage.co.uk